FAQs - Hardwood Flooring
GENERAL - Hardwood Flooring
Yes an Yes:
Johnson Hardwood abides by stringent local forest management rules, and supports sustainable practices by planting three trees for every one that is harvested. At least 30-percent of the logs harvested by Johnson Hardwood are from trees that have already died due to a variety of natural causes, most commonly old age or storm damage. Most of our harvested trees are over 100-years old, and harvested to keep the forest healthy since aged trees release less oxygen and block sunlight essential for the growth of younger trees.
LACEY ACT FOR RESPONSIBLE FORESTRY & SUSTAINABILITY
Johnson Hardwood aims to assure our customers that the Johnson Hardwood floor they’ve purchased comes from responsibly harvested forests. Johnson Hardwood sources hardwood from the U.S., China, Brazil, and Canada. Government regulations in all of these countries have become much more stringent over the last decade, and we fully support their efforts to protect their forests. China’s Council for International Cooperation on Environment and Development regulates sustainable development through environmental policy and reform. There are Six National Key Forest Programs regulated by China’s State Council that include the promotion of economic development, natural resource management and environmental protection, taxation and regulation of timber markets, and international trade and investment. To comply with global sustainability, Brazil adheres to forest certification as regulated by the Forest Stewardship Council. Canada’s forest and lumber industry is regulated by the Canada Environmental Protection Agency. The United States, through the enactment of the Lacey Act, has helped other countries by preventing the importation of any hardwood product that is not legally harvested according to the rules of its country of origin. The Lacey Act requires end users of endangered wood to certify the legality of their supply chain all the way to the trees. If an importer knowingly imports tainted wood that has been illegally cut down for lumber then they will be raided by the Environmental Investigation Agency and dealt with by the U.S. Department of Justice.
Refer to the following table for a list of Johnson Hardwood products, wood species classifications, and their countries of origin.
It is part of the Johnson Hardwood manufacturing process to carefully craft and comply with the most stringent wood manufacturing regulations imposed in the United States. The most stringent standard being CARB compliant according to the California Environmental Protection Agency. CARB refers to the California Air Resources Board as governed by the California Environmental Protection Agency. CARB’s mission is to promote and protect public health, welfare, and ecological resources through effective reduction of air pollution. Since January 1, 2009, manufacturers of wood products are required to prove their products meet the established Airborne Toxic Control Measure (ATCM) that sets upper limits on formaldehyde emissions from composite wood products sold in California, and is the most stringent due to the emission caps where other standards are based on averages. To be compliant, Johnson Hardwood is required to provide documentation of compliance and label products accordingly. CARB II, effective January 1, 2011, has defined guidelines for the entire production process that includes the manufacturer, distributor and fabricator of wood products.
For more information, please visit the California Air Resource Board’s website @ ww2.arb.ca.gov
Solid wood flooring is categorized as strips (Under 3” in width) and planks (3” and wider) which are cut from a solid piece of wood. Engineered wood flooring usually consists of a plywood core which utilizes individual plies (Lamellas) which are usually comprised of one or two of the following wood species: Baltic Birch, Poplar, Eucalyptus, Red Oak, White Oak or Meranti. On a lesser scale, fillets and/or MDF (Medium Density Fiber Board) or HDF (High Density Fiber Board) is also used to make up the core material for engineered wood flooring. Lastly, engineered wood flooring is comprised of a ware-layer (Decorative top layer of any given specie of wood), which can range in thickness from .4 mm up to 7 mm.
PRE-FINISHED SOLID
Pros: ¾ solid (Strips or Planks) wood flooring has an average serviceable life span of approximately 40 to 100 years. ¾” solid wood flooring can be refinished an average of 4 to 5 times throughout its serviceable life span. ¾” solid wood floors can increase the resale value of your home. Solid prefinished wood flooring is available in array of colors, as well as texture types such as wire brush, hand-scrap, pillowed edge, traditional square edge, bevel edge, micro-bevel and/or smooth finish so as to complement your chosen interior design. One benefit of smooth finish solid wood flooring is that it is considered to be Hypoallergenic.
Cons: ¾” solid (Strip or Plank) wood flooring requires a wood subfloor as said type flooring requires mechanical attachment via flooring cleats or flooring staples. As a general rule, installation of ¾” solid (Strip or Plank) flooring via the glue down method of attachment is not recommended. Solid (Strip or Plank) wood flooring can be less dimensionally stable compared to engineered wood flooring. Solid (strip or plank) flooring is not recommended for below grade installations.
PRE-FINISHED ENGINEERED
Pros: Average serviceable life span can range from 20 to 40 years. Planks can be manufactured to wider widths than solid wood planks because of the superior dimensional stability of engineered wood flooring. Engineered wood flooring can be installed on grade, above grade and below grade. Engineered wood flooring can floated, glued down or mechanically fastened via flooring cleats or flooring staples. Engineered wood flooring is considered environmentally friendly in that the manufacturing process can produce multiple ware-layers out of a solid ¾” thick plank compared to solid wood flooring which only yields a single plank. Engineered wood flooring is typically less expensive than solid wood flooring. Engineered wood floor is relatively easy to install, which makes it a perfect choice for a DIY project. Engineered wood flooring is more resistant to fluctuations in temperature and humidity than solid wood flooring.
Cons: On average, engineered wood flooring has a shorter serviceable life span compared to solid wood flooring.
PREFINISHED wood flooring is stained and finished by the manufacturer so when you receive the flooring it is ready to be installed (Note: Always follow manufactures requirements for pre-installation acclimation). This is a major benefit as there is no extra costs associated with job site sanding, staining and finishing.
Pros: There is no sanding mess to deal with, not to mention you save time in not having to sand the floor.
UNFINISHED wood flooring does not come prefinished from the manufacturer, but rather is sanded, stained and finished at the job site, usually by a wood flooring contractor who is well trained in installation/sand and finish. Cost more to sand, stain and finish the floor than a prefinished floor. The overall process takes longer because of the need to sand, stain and finish the flooring after being installed.
Pros: End-user can choose custom colors, as well as custom designs.
The primary reason for adding aluminum oxide to a finish is to promote ware through resistance, which helps to extend the life of the floor.
Yes, through advancements in finish technology we have finishes that provide superior ware through protection.
Ambient conditions of 60 – 80 Fahrenheit and a relative humidity of 35 to 55 % (which equates to 6.8 to 10.2 % moisture content which is the moisture content range created during the manufacturing process) must be established and maintained for a minimum of five days prior to the delivery of the flooring material to the job site, then maintained during the acclimation process, as well as during the installation process for the life of the installation. You can download a copy of our installation guidelines and warranty information by clicking on the links below.
- ENGINEERED HARDWOOD
Installation Guidelines
Warranty Information - SOLID HARDWOOD
Installation Guidelines
Warranty Information
Square edge, standard bevel, micro-bevel, high low and pillowed.
Smooth, wire brush, hand scrape and/or a combination of wire brush and hand-scraped.
We recommend taking a small sample (10” to 12” long) of your wood floor to your local big box stores paint department where they can use a Spectrophotometer to identify the color make-up used to stain the flooring. Once they have the color recipe they can mix up a stain.
Yes, color comes from chemicals that the tree deposits in the cells as they change from heartwood to sapwood. Different trees produce different chemicals just as different people have different colored skin, hair, and eyes.
Yes, and the reason for this is that display samples compared to packaged flooring are commonly exposed to UV light which can lighten and/or darken wood over time as all wood species are photosensitive from one degree to another. As for packaged flooring it has yet to be exposed to UV light so the color tone is preserved. That being said, Johnson’s sales staff monitor display samples and when they find samples that have experienced color change and/or are damaged they replace them with a fresh sample.
This is quite normal as the flooring under the area rug was protected from exposure to UV light, which as we know, can/will lighten and/or darken wood as a result of the inner action between UV light and the chemicals found in wood.
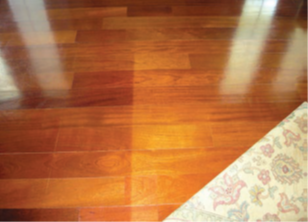
Cure: Exposing the wood covered by an area rug to UV light will eventually blend in the exposed wood with the wood protected from UV light.
SHOPPING
Unfortunately we do not sell direct to the public, but rather through flooring distributors as well as flooring retailers.
Johnson flooring products are available through your local participating retail flooring outlets.
Note: Please refer to Johnson’s web site for dealer locator information. Or, you may call Johnson’s Customer Service Department (626-363-9000) at which point a customer service representative can get you in touch with one of our sales agents who handles retail accounts in your area.
5% for a standard installation involving a single room. 7.5% for installations involving multiple intersecting rooms and 10% for floors installed on a 45 degree angle.
Note: It’s always a good idea to purchase an extra carton or two of material just in case the floor becomes damaged and you have to make repairs you have material from the same run which means the dye lot will be exactly the same as the installed wood, which means it will blend in with the existing floor, whereas flooring from a different run may not blend in as well.
INSTALLATION - Hardwood Flooring
Solid wood flooring is designed to be installed on grade and above grade. Engineered wood flooring is designed to be installed on grade, below grade and above grade.
Johnson’s solid wood flooring products cannot be installed over radiant heat type systems.
Johnson’s engineered wood flooring products can be installed over “hydronic” (hot water tubbing) in floor radiant heat type systems with the following exclusion: Hickory is not approved for installations over radiant systems of any kind.
Johnson Hardwood, has determined that WarmStep, Powered by FiberThermics is suitable for use in conjunction with our engineered hardwood flooring products (excluding hickory):
This approval is not a general endorsement of electric in- floor radiant heat systems but applies specifically to WarmStep by ThermoSoft. The approved products listed must be installed using Johnson Hardwood/National Wood Flooring Association (NWFA) and WarmStep approved installation methods.
Prefinished Solid: YES
Acclimation depends on geographic location, interior climate control and time of the year. The point of acclimating wood flooring before installation is to allow the moisture content of the wood to adjust to the installation sites “normal living conditions” which is interpreted to mean 35 to 55% relative humidity and 60 to 80 degrees Fahrenheit respectively. These conditions MUST have been established at least 5-days prior to delivering the flooring to the job-site and continue for the life of the floor. In addition, all doors and windows MUST be installed and weather striped prior to delivering the flooring to the job-site.
The worst-case scenario is one in which wood flooring is stored at the jobsite in an uncontrolled environment – especially one that is subject to excessive moisture and humidity conditions. It does no good at all –in fact it is likely harmful – to store wood flooring at the jobsite under conditions that do not reflect those normal environmental conditions. Garage and exterior patios, for example, are not acceptable areas to store wood flooring.
Wood flooring is a hygroscopic material subject to dimensional change because of variations in moisture, temperature and humidity in the surrounding environment. That has led to increasing awareness of the need to acclimate wood flooring before installation. Wood flooring simply needs to reach a moisture content level in equilibrium with the surrounding environment in which it will be installed, at or near normal living conditions. Always account for the time of year and geographic location.
Prefinished Engineered:
Johnson engineered wood floors do not require pre-installation acclimation for “any” specific amount of time. However, the environment MUST represent “normal live-in conditions” which is interpreted to mean an environment maintained at 35 to 55 percent relative humidity and a temperature of 60 to 80 degrees Fahrenheit respectively. These conditions MUST have been established at least 5-days prior to delivering the flooring to the job-site and continue for the life of the floor. In addition, all doors and windows MUST be installed and weather striped prior to delivering the flooring to the job-site.
We recommend FloorMuffler UltraSeal, which is a closed cell polypropylene foam that provides cushion along with moisture vapor protection. (And/or any closed cell type underlayment pad which does not exceed 2 mm in thickness). NOTE: Properly attached 1/8” – ¼” and/or 1/2” cork is an acceptable underlayment type material as long as it is properly adhered to the subfloor/substrate according to the cork and/or adhesive manufacturer’s guidelines.
Yes, we have a wide variety of trims and moldings to fit each and every need.
There are numerous manufacturers’ of high quality urethane base adhesives available to the flooring professional and/or DIY to choose from. They include (but are not limited too): Franklin Titebond, DriTac, Sika, Stauf and Bostik Findley, just to name a few of the nationally recognized brands. For additional information on adhesive/vapor retarder requirements, please refer to Johnson’s installation instructions which are available on Johnson’s web site johnsonhardwood.com.
Check with the adhesive manufacturer as most adhesive manufacturers’ will not offer warranty protection against adhesion bond failure. The reason for this is due to the wax coating applied to the exterior side of the OSB panels so as to help repel moisture so that it’s not absorbed into the shear wall, which could lead to decompression of the strands and/or the development of microbial growth.
No, for the wood flooring material to be soundly attached and prevent vertical movement/deflection, said type subfloor systems require the addition of ¾” X 4’ X 8’ solid CDX/ACX plywood panels. For further information, please contact Johnson’s Technical Department at 800-910-3047.
Yes, both solid and engineered wood flooring planks can be replaced with minimal effort. For further information on replacing planks, please contact Johnson’s Technical Department at 800-910-3047.
Yes, and you can find a step by step process for touching up scratches, which is available in our Care and Maintenance guidelines at johnsonhardwood.com
We do not recommend taking on such tasks, as it takes many years of hands on experience to achieve a level of expertise required to properly sand, stain, finish and/or recoat wood flooring as there are many steps the flooring professional must undertake to end up with a beautiful looking floor. Not to mention the sanding equipment is extremely expensive and must be maintained in order for the machinery to perform at its peak level, which you will not get with rented machinery.
Yes, in most cases it can, but the flooring installer must consult with the adhesive manufacturer’s Technical Department before moving forward with the installation as they will have questions pertaining to the type of vinyl it is and the way in which it was installed.
We do not recommend installing our wood flooring products (solid or engineered) in a fully functional bathroom (i.e., one which contains a shower, a steamer and/or bath tube). The reason for this is that the high relative humidity and/or direct water contact with the floor can/will result in irreversible damage to the floor. That being said, our wood flooring products are a good choice for powder room applications.
Scotch 2080 for Delicate Surfaces. This is the only tape approved for Johnson wood flooring products.
TAPE REMOVAL TIPS: Lift it up by slowly pulling it back on itself, at a 45-degree angle.
Note: Lifting the tape straight up can result in finish release which would not be covered under Johnson’s finish warranty.
CARE AND MAINTENANCE - Hardwood Flooring
No, we do not recommend the use of carpet type vacuums to vacuum your wood floor as the beater bar can/will mar the protective urethane finish over time and if this were to occur would not be covered under Johnson’s finish warranty.
That being said, what we do recommend is a canister type vacuum (such as the Miele brand) with soft rubber wheels that won’t scratch the finish, along with a soft China bristle attachment that will not harm the floors protective finish.
No, we do not recommend the use of steam cleaners as they can/will (over time) damage your floor (i.e., cause the finish to blush, result in finish and/or ware-layer checking, finish degradation resulting in flaking and/or peeling of the finish, distortion of the ware-layer and/or separation of the cross plies due to rolling shear), which if any of the aforementioned conditions were to occur, would not be covered under any/all applicable warranty coverage offer by Johnson.
We recommend placing protective felt glides on the bottom of furniture posts/legs and/or bases. Note: Protective felt glides can be purchase at your local big box stores or online.
No, Johnson does not recommend the use of area rugs containing a continuous solid rubber backer as they have been known to trap moisture between the surface of the wood floor and bottom of the rubber pad connected to the rug, which can result in moisture caused degradation to the finish and/or in between plies that make up the plywood core. In addition, we do not recommend the use of gel type mats/pads being placed over the surface of any/all Johnson wood flooring products for the above stated reasons.
We recommend non-slip pads such as: Veken Non-Slip Extra Thick Gripper for Any Hard Surface – Gorilla Grip Original Area Rug Gripper Pad. And/or Grip Master 2X Extra Thick Area Rug Pad. Note: The aforementioned pads are available through Amazon.com.
We recommend Bona Wood Flooring Cleaner and/or Basic Coatings Squeaky Clean, which can be purchased at your local big box stores, or on line. Note: Do NOT apply wax coatings of any kind, products containing silicone oils, renovators, rejuvenators, lemon oil, oil soaps, solvents, Windex and water, water, Pine sol and/or like type products, citrus base products, End-Dust and/or any other cleaning/maintenance type products that were not previously mentioned.
COMMON PROBLEMS AND THEIR CAUSES - Hardwood Flooring
The truth of the matter is that it comes down to customer expectations and/or the way in which the flooring was presented to you by the retailer (i.e., you may have been told this flooring is bullet proof as the finish contains aluminum oxide which makes it ding, dent and scratch proof).
Note: Wood flooring is available in a wide verity of wood species which have their own unique hardness rating based on the Janka Hardness Scale. The scale ranges from as low as 100 to a high of approximately 3,800. The ironic thing is that both the low and high ratings come from hardwoods (Deciduous Trees), which most people equate all hardwoods to be strong and after undergoing the finishing process evenly durable. Well that’s simply not the case, as we know that different species have different densities which produce different Janka Hardness Ratings…some lower and some higher.
Bottom line is, ALL wood species will experience denting and/or scratching (from one degree to another while in service), so when choosing a wood floor you should consider the following: Do I have an active family (i.e., small children who are more likely to drop objects that can damage the floor and/or have pets such as a dog(s) who’s claws could possibly cause scratches, indentations and/or chipping to the protective finish and/or wood fibers)? Do I live in an area where I might be dragging sand particulates into the house and onto the floors, which can/will scratch the floors finish? If you answer yes to either of these questions it will help you to make better decisions when choosing a floor, like choosing a textured floor like a hand scrapped product over a smooth finish floor as the hand scrapping will hide dings, dents and scratches better that a smooth finish floor.
There are several factors that can cause wood floors to become dull and hazy:
- The cleaning applicator (typically a micro-fiber) has become soiled and as a result is spreading a fine film of dirt over the floors surface. Note: Cleaning applicators should be changed out every 500 SQ FT so as to prevent a dirty hazy buildup from developing on the floors surface.
- The floor is being cleaned with an excessive amount of cleaner and over time this can lead to a dull hazy looking floor. Note: Follow the cleaner manufacturer’s directions as to the proper way in which to use their product.
- During the glue down process adhesive made its way onto the floors surface and was not thoroughly removed which resulted in a condition known as adhesive smear which causes the floor to look dull and hazy no matter how much you try and clean it. Note: Contact the adhesive manufacture as they’ll be able to provide recommendations as to the best way to safely remove adhesive smear/residue without damaging the floors protective finish.
- Using non recommended unauthorized cleaning products that contain vegetable oil, silicone oil, oil soaps, citrus oils, waxes and/or any type of cleaner that can/will leave a dull/hazy residue. Note: Use only cleaning products recommended by Johnson.
- Using tap water that has a high mineral content will result in mineral build up which can/will cause the floor to look dull and hazy. Note: Do not use water to clean your wood floors as it can/will result in irreversible damage to the floor, which will not be covered under any/all applicable warranty coverage offered by Johnson.
- Using a steam cleaner to clean wood floors can/will result in a dull/hazy looking floor, not to mention other destructive damage that can/will result in irreversible damage to the floor, which will not be covered under any/all applicable warranty coverage offer by Johnson.
Unfortunately we (the wood flooring industry) hear of this concern quite too often, especially when it comes to consumers who have not been instructed on how to properly clean their wood floor (i.e., smooth surface floors compared to textured wood flooring surfaces).
Moving forward it is important to know why said type condition occurred in the first place. And, what can be done to help prevent it from occurring with future cleanings?
Cause: Micro-fiber cleaning pads and/or cleaning cloths are designed to trap dust film into their specially designed fibers, which “unfortunately” can catch on the woods Run-Out Grain (Note: Run-Out Grain is the point where the woods annual growth ring runs out the side edge of the plank), which can result in wood fiber tear-out AKA as splinter tear outs.
Cure: For minor slivers/splinters along the edges of boards, carefully shave off with a razor knife, then touch-up as necessary. Or, Replacement of affected boards may be necessary in some cases.
Preventative Measures: We recommend cleaning the floor at an angle (approximately 30 to 45 degrees) rather than with the grain, by doing so can/will lessen the chance of the micro-fibers and/or cloth catching on the woods Run-Out Grain and tearing loose from the board in the form of splinters.
(Example: Wood fiber tear-out caused by a micro-fiber snagging on the woods run-out grain)
Unfortunately when we perform a site inspection involving the aforementioned conditions we discover the root cause as being site and/or installation related. However, on rare occasions, said type conditions can be associated to manufacturing as the cause. Please see below for an explanation as to the causes for the aforementioned conditions:
Squeaking: Said type condition occurs from vertical movement of the individual flooring planks when walked upon, which causes the edges to rub together resulting in a squeaking type sound. Note: Said type condition is consistent with an improper fastening schedule (Too few fasteners spaced too far apart) – Loose subfloor system – Using the wrong gage fastener (i.e., too thick) thereby breaking the tongues which can/will lead to vertical movement and the rubbing of planks thereby causes a crackling and/or squeaking sound – Subfloor that is outside the manufacturers required flatness tolerance – Mechanically fastened flooring that was installed over an underlayment pad – Floating floors over to thick of an underlayment pad (i.e., pads that exceed 2 mm in thickness) can/will result in to much vertical movement thereby causing the planks edges to rub against one another resulting in squeaking and/or a crackling sound – Improper trowel size/configuration which results in an insufficient amount of adhesive between the finished wood floor and the subfloor/substrate, which can result in a weakened bond leading to vertical movement and a squeaky floor – Flooring adhesive applied over a contaminated subfloor/substrate resulting in adhesion bond failure, which can/will result in vertical movement of the flooring planks resulting in rubbing of planks thereby causes a squeaking type sound – Not maintaining ambient conditions within the range as per the installation/guidelines – Flooring impingement as a result of cutting the flooring tight to vertical obstructions.
Popping: Said type condition is typically associated with glue down installations. The popping sound is the result of a momentary stick and release of the adhesive/plank to a low spot within the surface of a subfloor (usually concrete but can occur over plywood and/or OSB subflooring as well). Note: Check for incorrect trowel size and/or configuration used to apply the adhesive (i.e., one that applies to little adhesive) – Surface contamination not removed prior to applying adhesive, which prevents the adhesive from properly adhering to the substrate and/or subfloor. In Addition, popping can also occur with flooring mechanically fastened to the plywood and/or OSB where 15 lb or 30 lb tar saturated felt paper was used as a vapor retarder and in those areas where the plank(s) span a low spot and when walked upon pushes the plank(s) against the tar saturated paper which can/will result and stick and release which can/will produce in a popping sound – Said type condition is also consistent with an improper fastening schedule (Too few fasteners spaced to far apart and/or the use of the wrong type of fastener).
Crackling: Said type condition can occur with floors installed in an uncontrolled environment. Note: If the relative humidity (within the structure) increases above the “maximum” stated range the individual planks will expand resulting in pressure buildup between planks, which is released when the floor is walked upon or when the ambient conditions return to a normal range as stated in the installation guidelines. Note: Crackling sound caused by an uncontrolled environment is most noticeable when walking on the floor in the middle of the night, or first thing in the morning – Mechanically fastening a wood floor over a pad can/will prevent a firm attachment to the plywood/OSB subfloor, which can/will allow the individual planks to move in a vertical direction resulting in planks rubbing together and/or wood fibers rubbing against the fasteners resulting in a crackling and/or squeaking sound – Glue down installations over gypsum and/or lightweight cement/concrete that was not properly prepared according the adhesive manufacturers guidelines and as a result did not adequately adhere to the substrate which can/will result in a crackling sound when walking upon the floor – Mechanically fastening a wood floor over a particle board subfloor thereby producing a weak attachment – Using the wrong gauge fasteners (too thick or too thin) thereby breaking the tongues and/or lack of fasteners to securely hold the planks tight to the subfloor which can/will lead to vertical movement and the rubbing of planks thereby causes a crackling and/or squeaking sound – Said type condition is also consistent with an improper fastening schedule (Fasteners spaced to far apart). Please refer to Johnson’s installation guidelines for proper fastening schedule for both our solid and engineered wood flooring products.
First off we need to know which installation method was used to install the flooring so that we can address the most common reasons why the floor sounds hollow (in spots or throughout) when walked upon:
Nail-down applications:
- Subfloor flatness does not conform to manufactures/industry (National Wood the surface of the subfloor and the bottom of the finished wood floor, which can/will produce a hollow sound when walking upon the affected area(s).
- A subfloor that is attached to a joist system might have been compromised at some point which resulted in a fracture/broken joist which can result in deflection of the flooring in the affected area can produce a hollow sound when walking upon the floor.
- Installing an engineered wood floor over an unapproved subfloor such as diagonally laid 1”X 6” planks and/or particle board can/will result in a loosely laid floor that can/will produce a hollow sound when walking upon the floor.
- Not using the required fastener as per the manufactures specification and/or not following the required fastening schedule can/will result in a loosely laid floor that can/will produce a hollow sound when walking upon the floor.
- Skip nailing rows and/or sections of flooring can/will result in a loosely laid floor that will produce a hollow sound when walking upon the affected areas.
Glue-down applications:
- Subfloor flatness does not conform to manufactures/industry (National Wood Flooring Association) specifications which can result in voids between the surface of the subfloor and the bottom of the finished wood floor which can/will produce a hollow sound when walking upon the affected area(s).
- Gluing down engineered wood flooring over an Oriented Strand Board (OSB) subfloor that contains a wax coating can result in the release of planks due to the wax acting as a bond breaker which if this were to occur, can/will produce a hollow sound when walking on the affected area(s). NOTE: Most adhesive manufactures’ (including Johnson Premium Hardwood) will not warranty their adhesive products against bond failure when used to attach wood flooring to OSB.
- Gluing down engineered wood flooring over subflooring and/or a concrete slab that has not been properly prepped as per the adhesive manufacturers guidelines (i.e., a dirty surface such as drywall dust and/or mud, paint over-spray, curing agents, cut-back adhesive residue, left over adhesive residue from a prior installation, failure to address moisture emitting from the concrete slab and/or alkali build up on the surface of the slab that was not neutralized prior to the floor being installed, can/will produce a hollow sound when walking on areas of the floor that have experienced adhesive bond release.
- Using a trowel configuration not specified by the adhesive manufacturer which spreads out an inadequate amount of adhesive (too little) needed to securely bond the flooring to the surface of the subfloor and/or concrete slab, can/will result in areas of inadequate bond which can/will produce a hollow sound when walking on the affected area(s).
- Allowing the adhesive to overly dry from the time of application to the time of placing the planks into the adhesive, which if were to occur, can/will result in a lack of transfer of the dry, skinned over adhesive from the substrate and/or subfloor to the back side of the wood flooring planks.
- Flooring Association) specifications (i.e., 3/16” in 10’ in all directions) which can result in voids between
There are several reasons that can cause a floor to become discolored:
- Excessive moisture emitting from the surface of a concrete slab which exceeds the ability of the moisture vapor retarder and/or hybrid adhesive (2 in 1 type adhesive if one was used) to adequately protect the floor from excessive moisture accumulation, which can/will result in discoloration of the floor in areas of high moisture concentration.
- Rust from the fasteners or metal shavings. (See Iron Stains.)
- Plant pots or other containers in direct contact with the floor, exposing the floor to topical moisture and/or condensation.
- Pet feces and urine stains. (See Chemical Stains.)
- Mildew-related stains – typically black in color.
- Decay-related stains – typically brown/white in color.
- Fungus or mold-related stains – typically grey, black, blue, or orange in color.
- Alkaline conditions – typically white, brown, or even grey/black in color.
- Moisture from below can cause dark staining, or a white haze between seams and on the surface of the wood.
- Topical moisture (incompatible maintenance products, spills, steam, etc.) can cause blushing or damage to the finish itself.
- Tannic acid present in some wood species is water- soluble and may discolor when it gets in contact with iron and water, which usually appears as a bluish/grey discoloration on the wood.
This condition is known as end-joint peaking, ski and/or end-lift and is the result of compression stress brought on by lengthwise expansion of the planks, which is due to a gain in moisture content after the flooring was installed. The following are the most common causes for said type condition:
- Flooring incompatible with the environment in which it is installed.
- Engineered flooring that has experienced an increase in moisture, where the core material running perpendicular to the face of the board swells at a different rate and in a different direction than the adjoining layers, forcing the ends of the material to lift, which can then telegraph to the surface of the plank.
- Inadequate or inoperable HVAC systems resulting in elevated humidity levels. (See Greenhouse Effect.)
- Improperly selected, improperly installed, or improperly applied moisture control systems (vapor retarders) that do not provide adequate protection from below the floor.
- Maintenance-related:
– Wet-mopping resulting in standing/topical liquid moisture left on the floor.
– Use of steam mops/cleaning devices.
– Use of non-breathable rugs on the floor.
– Not maintaining relative humidity levels year-round to support the installed flooring.
(Example: End-Joint Peaking, Ski and/or End Lift)
Dry Cupping
Definition: A concave or dished appearance of individual engineered flooring planks with the edges raised higher than the center.
- When relative humidity levels remain below the manufacturer’s recommendations for long enough, engineered planks can begin to dry cup. When this happens, the wear layer loses moisture and begins to shrink across its outer face, which can exert enough force on the core material to pull the edges of the plank (often the groove side) upward. This causes a cupped appearance across the width of the board.
- In severe cases, layers within the plank may separate from one another when stresses exceed the strength of the wood flooring material itself, resulting in ply separation. This is most common in dry regions and during dry seasons.
(Example: Dry Cupping)
Delamination/Glue-Line Separation (Engineered Wood Flooring)
Definition: Engineered flooring is manufactured by adhering several layers/plies together. The separation of two layers/plies within a piece of engineered flooring due to the lack of an adhesive bond is typically identified as a clean separation at the glue-line. Adhesive bond failure is unrelated to inadequate relative humidity levels.
Causes:
- Manufacturing-related:
– Veneers not bonded together due to improper or inadequate adhesive application, missing adhesive, dried, or uncured adhesive, or steam pockets.
- Site-related:
– Extended or repeated exposure to standing water (flooding).
(Example: Delamination)
Wood Shear (Engineered Wood Flooring)
Definition: External stresses exceeding the strength of the wood fibers within an individual plank of engineered flooring, resulting in the wood fibers being torn apart. When examining this type of failure in an engineered wood flooring plank, wood fibers will be visible at the point of separation, remaining bonded to the adhesive layer.
Causes:
- Layers within the plank shrink or swell excessively because of low relative humidity or excessive moisture (outside of manufacturer’s recommendations), thereby creating excessive force on opposing layers sufficient enough to tear the wood fibers apart.
- Inadequate or inoperable HVAC systems resulting in elevated humidity levels.
(Example: Wood Shear/Rolling Shear)
Definition: A separation of the wood’s fibers along the grain (parallel to the growth rings), that usually occurs between the rings of annual growth.
Causes:
- Can be the result of any of the following in the standing tree:
– Gale or hurricane-force winds.
– Tree wound.
– Tree age.
– Site and environmental conditions.
– Wood structure and chemical composition.
- Damage that can be caused during the felling of the tree.
- Changes in environmental conditions can expose existing shake when it was not visible at the time of grading or installation.
- During the finishing process, when water popping, using chemical-reactive conditioners, water-based stains or water-based finish products (sealer, finish, or stain) on a newly sanded wood floor, the wood surface and exposed fibers are hydrated resulting in grain raise, which can “lift or distort” the edge of previously concealed shake, not visible at the time of grading or installation.
- Site conditions on factory finishes can expose existing shake when it was not visible at the time of grading or installation.
Cure: In factory-finished flooring, replacement of the affected plank is typically the recommended remedy.
(Example: Shake – Ring Shake/Ruptured Grain)
Lathe Checks (Rotary Peeled/ Sliced Engineered Flooring)
- Lathe checks may become apparent/transfer to the surface with failure to maintain the ambient interior conditions specified by the manufacturer for the life of the product through all seasons. Loss of moisture or inadequate conditions post-manufacture can expose/generate fractures in the face veneer/lamina at any time.
- Excessive and rapid fluctuating environmental conditions from above or below the floor can cause stresses in the veneers sufficient enough to cause fractures in face veneer at any time.
(Example: Lathe Checks/Surface Checks)
Definition: A tearing apart or rupturing of the wood that may run at various angles to the growth rings.
Causes:
- Mechanical damage caused by a variety of potential sources including:
– Damage from when the tree hits the ground as it is felled during harvest.
– Mishandling of the product in the factory, during transport, or during installation, such as when the product is dropped, banged, or in other ways damaged.
– Overdriven or improper fasteners can split or crack the tongue as a result of incorrect air compressor pressure settings.
– Too close of a fastener schedule.
- Splits or cracks may become apparent with a loss of moisture content, usually as a result of a reduction in relative humidity or extreme dry conditions (low RH), exposing prior damage to the wood.
- Splits/cracks may telegraph through to the finished surface of the wood causing less elastic finishes to display fine linear cracks in the surface of the finish film precisely in the same location as the underlying anomaly.
(Example: Splits/Cracks)
Definition: Gaps that appear between individual boards, opening and closing with seasonal humidity changes. Wider boards can experience wider gaps. Gap size is directly related and proportional to the board width.
Causes:
- Most normal gaps are caused by seasonal fluctuations in relative humidity. The floor expands with high humidity and contracts with periods of low humidity. This type of expansion and contraction is considered to be normal and expected with wood floors when exposed to seasonal variations.
- When wood flooring is installed during dry seasons where relative humidity is not maintained, it is normal to leave internal expansion spaces/gaps (washer rows) within the floor to accommodate for seasonal humidity changes.
(Example: Seasonal/Normal Gaps)
Definition: Gaps between abutting wood floor boards in the installed floor that were not intentionally placed and remain with seasonal fluctuations in moisture and humidity.
Causes:
- Flooring not installed tightly together.
- Debris between the boards during installation.
- Solid wood flooring installed at higher moisture content than what the normal, in-service conditions can support.
- Inadequate or inoperable HVAC systems resulting in elevated humidity levels. (See Greenhouse Effect.)
- Edge-crush/compression-set from exposure to extreme moisture after the floor was installed.
- Distorted wood flooring from the manufacturing process (such as crook, pistol-grip, end joints out-of-square, etc.) or from a gain/loss in moisture (such as end-swell/flared-ends or any form of warp) that causes gaps between boards during installation.
- Subfloor-related:
– Loss of fastener holding power as a result of reduction in moisture within the wood
subflooring system.
– Wood subflooring with excessive moisture during wood floor installation. Gaps will be most noticeable at approximate intervals coinciding with the subfloor joints. (See Panelization.)
– Improper subflooring material that will not adequately hold fasteners.
– Substrate not flat to within required tolerance (See NWFA Wood Flooring Installation Guidelines for flatness requirements).
– Movement or deflection within the subflooring system.
– Weak subfloor or subfloor system.
– Structural, foundation, or support pillar settlement.
(Example: Abnormal Gaps)
Definition: A separation that occurs on the ends of two abutting wood floor boards.
Causes:
- Loss/gain of moisture in engineered flooring.
– Due to the construction of engineered flooring, each layer shrinks and swells in different directions and at different rates than the adjoining layers. It is common for it to shrink/swell in its length when exposed to changes in moisture content.
- Loss of moisture in solid flooring.
– Solid wood will generally only shrink/swell .1%-.2% its overall length with changes in moisture content. The pith of the tree may shrink/swell at higher rates.
- Flooring not installed tightly together.
- Debris between the boards during installation.
- End joints of flooring manufactured or cut out of square, or mis-milled tongue and groove profile.
- Subfloor-related:
– Movement within the subflooring system, and structural or foundation settlement.
– Wood subflooring with excessive moisture during wood floor installation.
– Wood flooring laid perpendicular to the direction of the wood subfloor material. Both plywood and OSB generally shrink/swell twice as much in width than in length.
- Nail-down floors:
– Debris between butt-ends of the boards during installation.
– Improper subflooring materials that will not hold the fastener.
– Wrong fastener used per flooring manufacturer.
- Glue-down floors:
– Early foot traffic before the adhesive has had time to set up during or following the installation.
– Improper use of straps or tape used during the installation.
– Incorrect adhesive used for the flooring being installed.
– Inadequate bond between the subfloor and the adhesive (poor preparation or incompatibility).
– Improper use of the adhesive.
º Wrong trowel or spread rate as required by the adhesive manufacturer.
º Inadequate adhesive transfer as required by the adhesive manufacturer.
º Improper flash time allowing adhesive to skin over.
º Not using a roller when recommended by the adhesive manufacturer.
- Floating floors:
– Failure to follow flooring manufacturer’s installation instructions.
– Improper acclimation/conditioning of the flooring and the building.
– Moisture or environmentally related issues.
– Inadequate perimeter expansion space at all vertical obstructions. The recommended expansion space may have been adequate at time of installation and closed due to environmental changes.
– Pinch points caused by door jams, baseboards, trim, or adhesive caulking restricting lateral movement.
– Heavy (or fixed in place) furniture restricting
lateral movement.
– Flooring length and/or width exceeding manufacturer’s requirements.
– Lack of, missing, or improperly installed transitions.
– Improper or missing glue used on tongue or groove of flooring.
– Improper glue application to tongue or groove.
– Loss of the glue bond between the tongue and groove.
– Broken or missing locking mechanism.
– Mechanical lock becomes disengaged. This is most common on end joints with deflection due to a subfloor out of flat tolerances or improper underlayment material.
– Improper underlayment material used (per the flooring manufacturer) below the flooring.
(Example: End-Gaps)
Hardwood Flooring
TECH TIPS
INTERNET SALES POLICY
Johnson Hardwood Internet Sales Policy
At Johnson Premium Hardwood Flooring, we are committed to manufacturing the finest hardwood flooring selections available. We believe consumers should utilize every resource available to assist with their selection of Johnson Hardwood products. Both Johnson Hardwood, and our dealer customers who have Johnson products on display, have made a significant investment in samples and other merchandising tools. This helps consumers to get a realistic look at the hardwood floor before making a purchase, and assists them to choose the right floor for their home. This selection process cannot be done with as much confidence over the Internet.
Therefore, we strongly recommend making your flooring purchases at dealers who have Johnson Hardwood products on display in their showrooms. Hardwood flooring is a significant investment, and our experience shows that a consumer can receive a higher value of service through a local flooring retailer.
However, we at Johnson Hardwood understand that many flooring dealers also promote Johnson Hardwood products through their websites. In order for Johnson Hardwood to offer warranty support and allow shipping flexibility we’ve developed the following parameters that we feel are critical to properly service our consumers. Following the suggested online selling parameters will guarantee full technical and claims support before, during, and after the sale. Please call (800) 910-3047 to verify that a dealer is approved for online sales of Johnson Hardwood products.
- Displayed pricing must not fall below the Minimum Advertised Pricing (MAP).
- We require that an online retailer has the ability to provide consumers with swatch or sample representations of color and texture to assist with their product selection and purchase.
- An online retailer must accept and agree to the Johnson Hardwood 25% restock fee for returns, and agree to our “no return” policy on molding.
- Should there be a product warranty claim resulting from an on-line sale; the retailer is responsible for inspection costs from an approved NWFA inspector.